Ergebnisse des Projektes
Continental
Die ganze Geschichte
Continental Trading GmbH – Der Kunde
Die Continental AG ist Marktführer der Automobilzuliefererbranche mit Sitz in Hannover. Sie entwickelte sich vom reinen Reifenhersteller zu einem der weltweit größten Anbieter von Bremssystemen, Systemen und Komponenten für Antriebe und Fahrwerk, Instrumentierung, Infotainment-Lösungen, Fahrzeugelektronik, Reifen und technischen Elastomer-Produkten. Dabei trägt Continental zu mehr Fahrsicherheit und zum globalen Klimaschutz bei.
Auf dem Betriebsgelände der Continental Automotive GmbH befindet sich auch die Continental Trading GmbH, welche der BU Commercial Vehicle & Aftermarket angehört und Trading sowie Aftermarket Produkte in die ganze Welt versendet.
Die Herausforderung: Auf einen Blick
Continental Trading GmbH – Die Herausforderung
Die Continental Trading GmbH in Babenhausen betreibt auf 9.320 m² ein Handelswarenlager für die Business Unit Commercial Vehicle & Aftermarket, von dem aus Produkte in die ganze Welt geliefert werden. Dazu sind automatische Hochregal-, Kleinteile- und Palettenläger im Einsatz, die über Förderstrecken teilweise miteinander verbunden sind.
4-gliedrige Systemlandschaft zur Steuerung der Intralogistik
Im Lager kommen SAP WM, ein speziell auf die Intralogistik konzipiertes Lagerverwaltungssystem (LVS) sowie ein Materialflussrechner (MFR) zum Einsatz. Das führende SAP-System erzeugt die Aufträge für die Intralogistik-Software, die im nächsten Schritt die Lageraufgaben ermittelt und an den MFR übergibt. Dieser übernimmt dann die Feinsteuerung der Anlagen über die S7-Steuerungen.
System als Black Box für SAP
SAP-seitig ist der bisherige Ablauf im Lager eine „Black Box“, d.h. dass das SAP-System erst mit Abschluss eines Lagerauftrags eine Rückmeldung über den Status des Auftrags erhält. Während der Auftrag im LVS bearbeitet wird, werden keine Daten über den Status mit SAP ausgetauscht – somit kann SAP-seitig nicht eingegriffen werden und beispielsweise die Priorität eines Auftrags verändern.
Modernisierung durch Retrofit mit SAP
Als im Rahmen einer konzernweiten Harmonisierung der Logistiksysteme das IT-Konzept für das Lager in Babenhausen bewertet wurde, wurde bei der Continental Trading GmbH entschieden, das bestehende System durch eine reine SAP-Lösung abzulösen, um sowohl die Komplexität der Systemlandschaft zu verringern als auch die Transparenz in der Intralogistik zu verbessern.
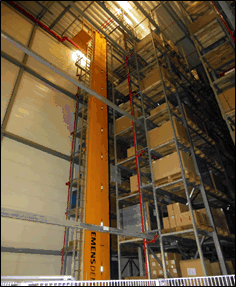
Continental
SAP Anlagen- und Behältersteuerung
Continental Trading GmbH – Das Projekt
Die SERKEM GmbH wurde als Partner für das Retrofitting der Intralogistiksoftware und Anlagensteuerung mit SAP ausgewählt. Continental entschied sich bei der Einführung des SAP Warehouse Management (WM)-Moduls für einen bewährten Partner, da SERKEM bereits bei Projekten an anderen Standorten von Continental den Logistikbereich betreute und so für Babenhausen auf ein bewährtes Grundtemplate zurückgegriffen werden konnte. Das Template beinhaltete bereits Stapler- und Scannerprozesse, Monitore für z.B. Lager und Versand sowie systemgestützte Verladeprozesse.
Die von SERKEM bei Continental in Babenhausen implementierte, native SAP WM-Lösung ersetzt nun vollständig das bestehende System der Intralogistik. Die automatisierten Komponenten des Lagers – AKL, HRL und Fördertechnik – werden nun direkt aus SAP angesteuert. Lediglich die einzelnen Aufträge werden durch einen Steuerrechner in Telegramme übersetzt. Alle Packstücke werden systemgestützt bewegt und der Status einer Lieferung ist jederzeit detailliert abrufbar. Die intralogistische Kette ist nun vom Wareneingang bis hin zur Auslieferung vollständig transparent in SAP abgebildet.
„Serkem ist ein flexibler, kompetenter und verlässlicher Partner, der aktuelle Probleme löst aber auch neue Themen anregt, mit Erfolg durchführt und im Tagesgeschäft begleitet.“
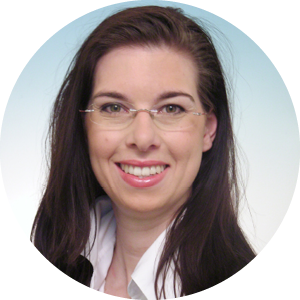